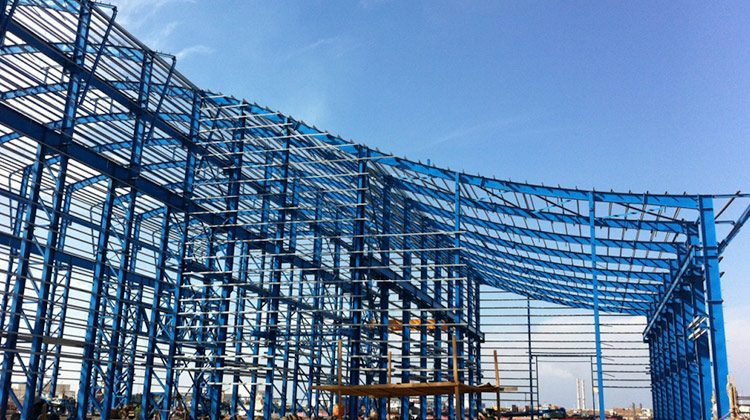
Steel Construction
- STEEL FRAME AND ROOFS:
Extreme care must be taken to ensure that the steel columns are in their exact position and vertically because it is impossible to fix later. Columns erected and fastened with bolts should not be left unsecured by braces. The construction and final connections of the upper parts are continued only after the columns are leveled, the concrete-steel connections (Bz) bolts are reinforced, the bottom plate is filled with mortar and the mortar dries. (Double nut should be preferred.)
In column-beam connections, it is useful to use a support bracket for ease of assembly and durability.
End-to-end joints should be reinforced with reinforcement plates to be placed on the sides and, if possible, at the top and bottom.
Wind and Earthquake connections should not remain inside the wall or plaster, 1-2 cm from the plaster. It should be arranged outside.
Oblique washers should be used to correct the flank bevel in the bolted connections of U, and I beams.
All free edges and corners are at least 3 mm. should be rounded to half diameter.
Especially in wide-span roof trusses and beams, giving the lower head a reverse slope should not be neglected.
In pipe productions, cracked pipes with water leakage can be used, not long and longitudinally. (The free ends must be sealed so that they do not rot from the inside).
Connecting the purlins to each other with bolts is easy in terms of assembly; where they sit on the truss, a support turbinate for the parts coming to the slope side provides benefits in terms of static.
- STAIRS, PLATFORMER, GUARDS:
It is useful to put an angle bracket under the lemon beam connection on sheet metal stairs. If there is no such detail in the project, the resources should be made up and down.
The exposed steel structure floors, platforms, and stair steps are sloped to prevent rain and washing water from collecting. (The same slope should not be neglected in concrete floors and foundations on which these types of structures sit).
50-60 cm. also, a transverse angle bracket et al. Protrusions with profiles should be arranged. To hold on, especially in shaky neighborhoods, a handrail should also be made.
Floor and platform space sides and stairs 90-110 cm. height railing is a must. The largest gap is 50-55 cm. There will be at least one horizontal member of the railing.
In pipe railings, struts and handrails are made of at least 1 1/4 finger pipe. Straight edges are brought to the inside of the railing profile irons. (In terms of ease of welding and smoothness, it is preferred that the inserted pipe be small in size since it is stuck. Otherwise, the tip of the stuck pipe will be slightly crushed).
In order to prevent missing and injured persons and tools, equipment, etc., from falling down, a maximum of 1 cm should be placed on the underside of the floor and platform railings from the floor. A (skirt) is set by leaving a space.
Instead of the cage, it starts at the height of 2.2-3 m. 6m from any ground. and for vertical ladders (Safety cage) reaching higher heights.
- RIVET AND BOLT WORKS:
Rivet and bolt holes are drilled. Punches can be used in holes up to 20 mm, provided that the difference between the upper and lower diameters does not exceed 1 mm, but the hole cannot be opened and widened by welding. Holes should not be larger than 2 mm from bolts and 1 mm from rivets.
When the two perforated pieces overlap, 2 mm from the project length from the hole, a thinner rod should be able to pass easily. Holes in this state can be aligned with the reamer. More confusing elements are replaced. (Or the hole can be filled and the additional plate welded and re-drilled).
- FLAGS (UNIFICATION PLATES):
Flags should be cut properly and should be ground when necessary.
No flag corners should be exposed in the knots. Care should be taken in the horizontal and vertical averages of the rectangular flag edges in the double diagonal middle knot.
If a flag is used in tubular productions, the pipe is slit, inserted into the plate, and welded on top and bottom.
- RESOURCES
Unless otherwise stated, only the electrical source is used.
Electrodes are selected according to the type of material to be welded. It should be kiln-dried before being used in cold and humid weather.
Roughness, slag, etc., on the surfaces, to be welded. There should be no imperfections and harmful substances such as oil, etc., should be thoroughly cleaned with sandpaper, wire brush, chisel, etc., just before welding.
It is essential to open a weld bead in stubble welds (edge to edge).
There should be no deformation after welding. For this, firstly, spot welding should be done mutually.
After welding, welds should be cleaned of slag with a hammer and arranged with chisels, grinding, etc., methods.
Visual smoothness and thickness of welds; Checking with a hammer for strength and cracking is usually sufficient. Important work is done with control (X-ray device).
Painting is not started until the welds are cleaned, arranged, and checked.